Digitalization of PILA POTŠTÁT s.r.o. using the HELIOS Easy information system + GATEMA WMS/MES
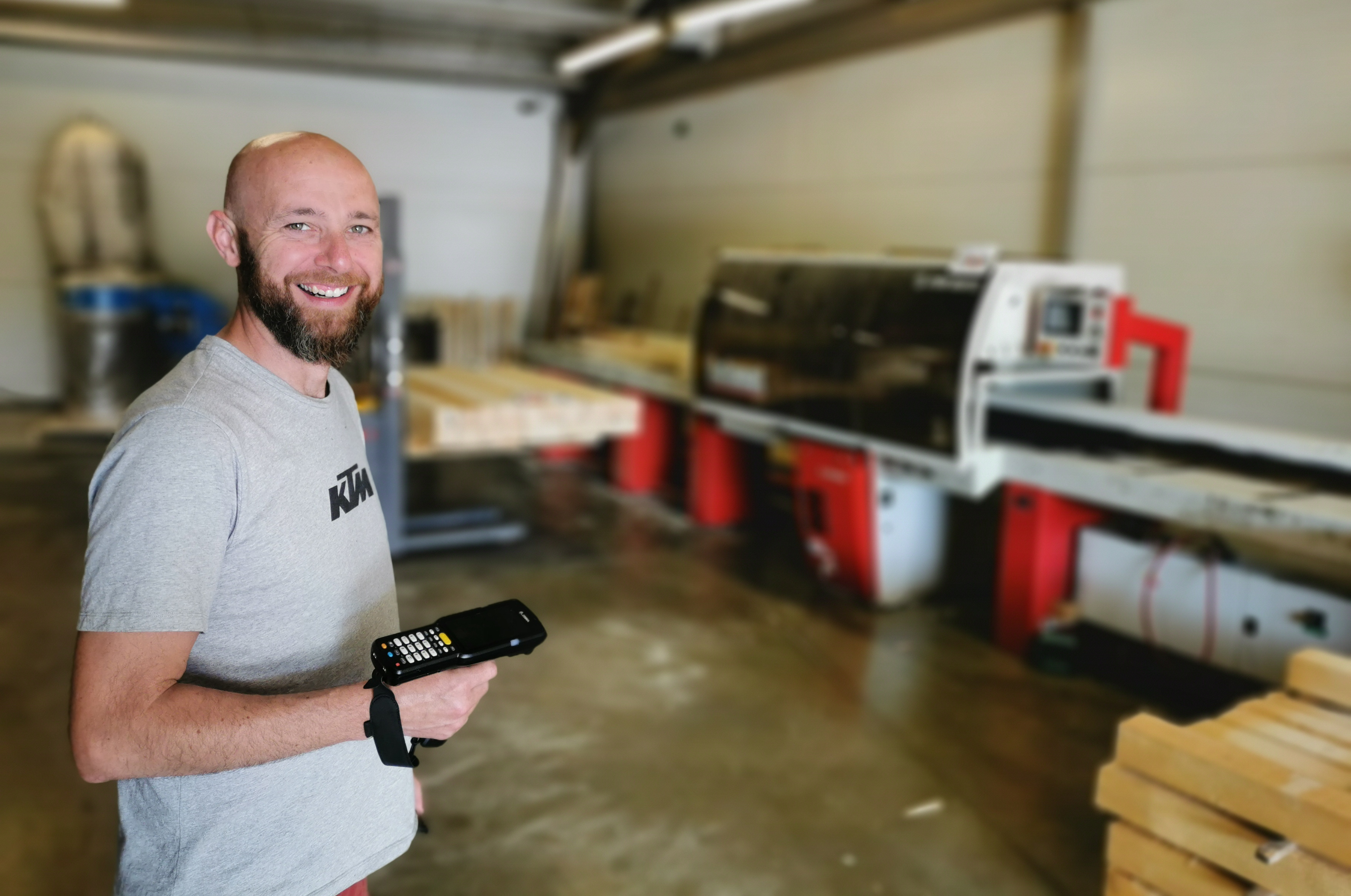
A case study of the introduction of HELIOS Easy into PILA POTŠTÁT s.r.o., where it supports order registration and production organization.
Intro
PILA POTŠTÁT s.r.o. is a manufacturer of wooden packaging and atypical pallets. It focuses on small batch production of pallets and wooden packaging with fast delivery. The company buys logs from which it produces its own lumber, which it treats and uses for its production.
The company employs approximately 30 people and has 2 large halls in two locations - a sawmill and a production and warehouse area where lumber is stored and heat treated, production takes place, and finished products are stored and shipped.
Records of orders and invoices issued and records of invoices received were kept in the HELIOS Red system. The company did not keep stock management, nor was there any production information system support. The accounting was handled externally.
The aim of the project was to implement a complete information system that would cover production, warehouses and orders and communicate with the accounting office (export of invoices received and issued). The requirement was also for a management interface and interfacing with the machines. Emphasis was also placed on data security.
HELIOS Easy was selected as the appropriate system, which is connected to the GATEMA MES production module and the GATEMA WMS mobile warehouse. The attendance system GIRITON was implemented, which is very well integrated with HELIOS.
The result is a robust solution that can support economic, commercial, warehouse and production processes.
Warehouse and sales
Invoices received are entered into the system. In order to record the status of payments of issued invoices, bank statements are processed. The Bank module is also used to create orders.
The Property module is used to record assets, especially machinery and tools.
Issued and received invoices are exported in the required structure to the accounting firm.
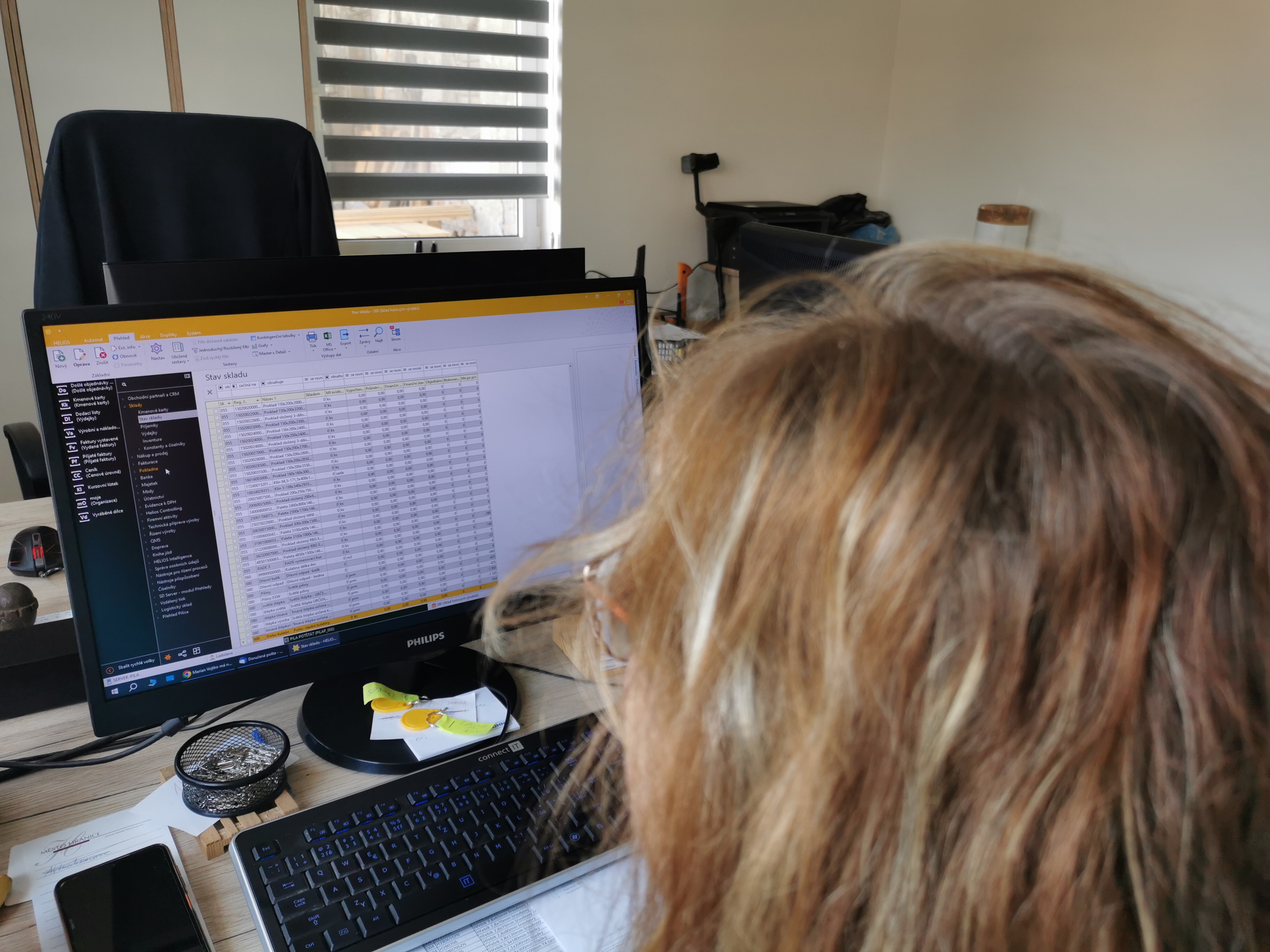
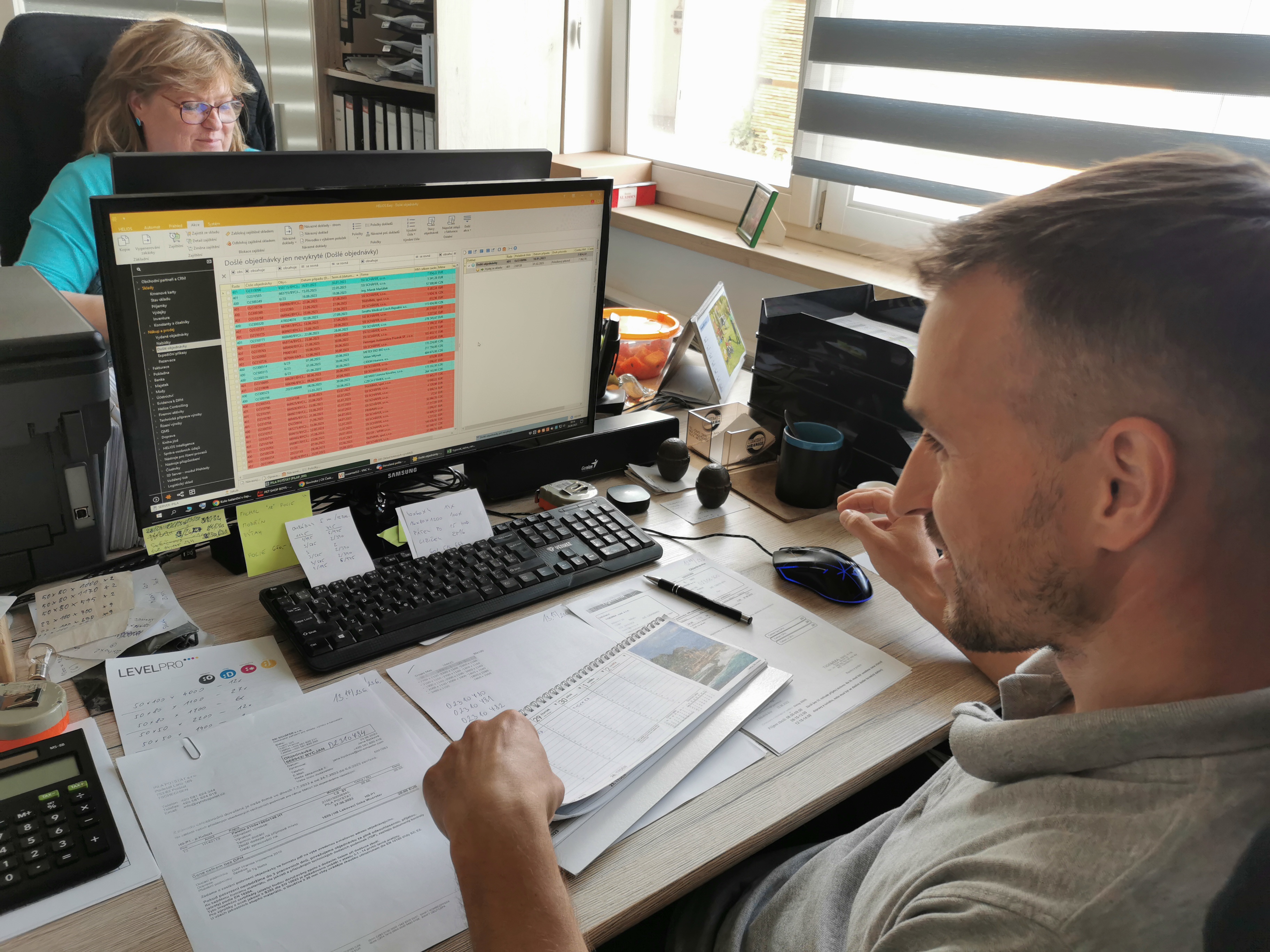
Order records (orders from customers) serve as the basis for production orders. Pricing is handled by means of customer price lists. Price lists are based on almost every customer. Orders are recorded both in CZK and EUR.
Three main warehouses are in place - a sawmill warehouse, a warehouse of treated and untreated lumber and a product warehouse. The other warehouses are used to record production material and components for production.
Receipts for production material (nails, screws) are generated from orders placed.
Loading of lumber, production components and finished products is done using the ETH 1022-100 take-off terminal and Zebra MC33N0G and Zebra MC33N0G mobile readers with longer range so that the barcode can be read directly from the forklift. Barcode readers attached to stationary terminals are also used.
Stock positions are supported. We work with individual pieces of lumber as well as with whole bales of lumber. The bales are marked with a barcode that carries information about the marking of the bale. The barcodes together with the marking of the lumber package (assortment + number of pieces) are printed on plastic labels and attached to the package.
The barcodes are also used to generate transfers between warehouses using mobile readers.
Production process
The production process begins in Pilnice during log processing. The logs are stripped of their bark and cut into planks and beams, resulting in bales into which the final product (sawn timber) is inserted.
Each bale is strapped and transported to the warehouse using an ETH terminal. The information system assigns it an identification - a barcode marking, which is automatically printed and pinned on the bale.
The debarker and band saw are connected to HELIOS, which displays data on the material being processed and the cutting yield.
The bales are transported to the production and storage location. Here, the bales of sawn timber are stored. Heat treatment is carried out on selected bales. The bales that are placed in the drying room are scanned by the forklift operator with a mobile reader.
A change in the treated/untreated status of the lumber results from the dispatch of an item of untreated material and the receipt into the same warehouse, but under a different product code representing the treated material. It still carries the bale number with it.
The next process already takes place with the support of the Manufacturing module. To work with the Manufacturing module, it was necessary to define the parts. A part is a designation for a manufactured semi-finished product or a product . Next, the material that is used for the production of the parts was defined. Using TPV, a technological procedure was created that contains the material required for the production of this part. A process drawing of the product is also available for the operator to view.
It is possible to have alternatives set in the technological process and in the materials used, and at the time of production planning the system has the possibility to select a suitable alternative according to the stock.
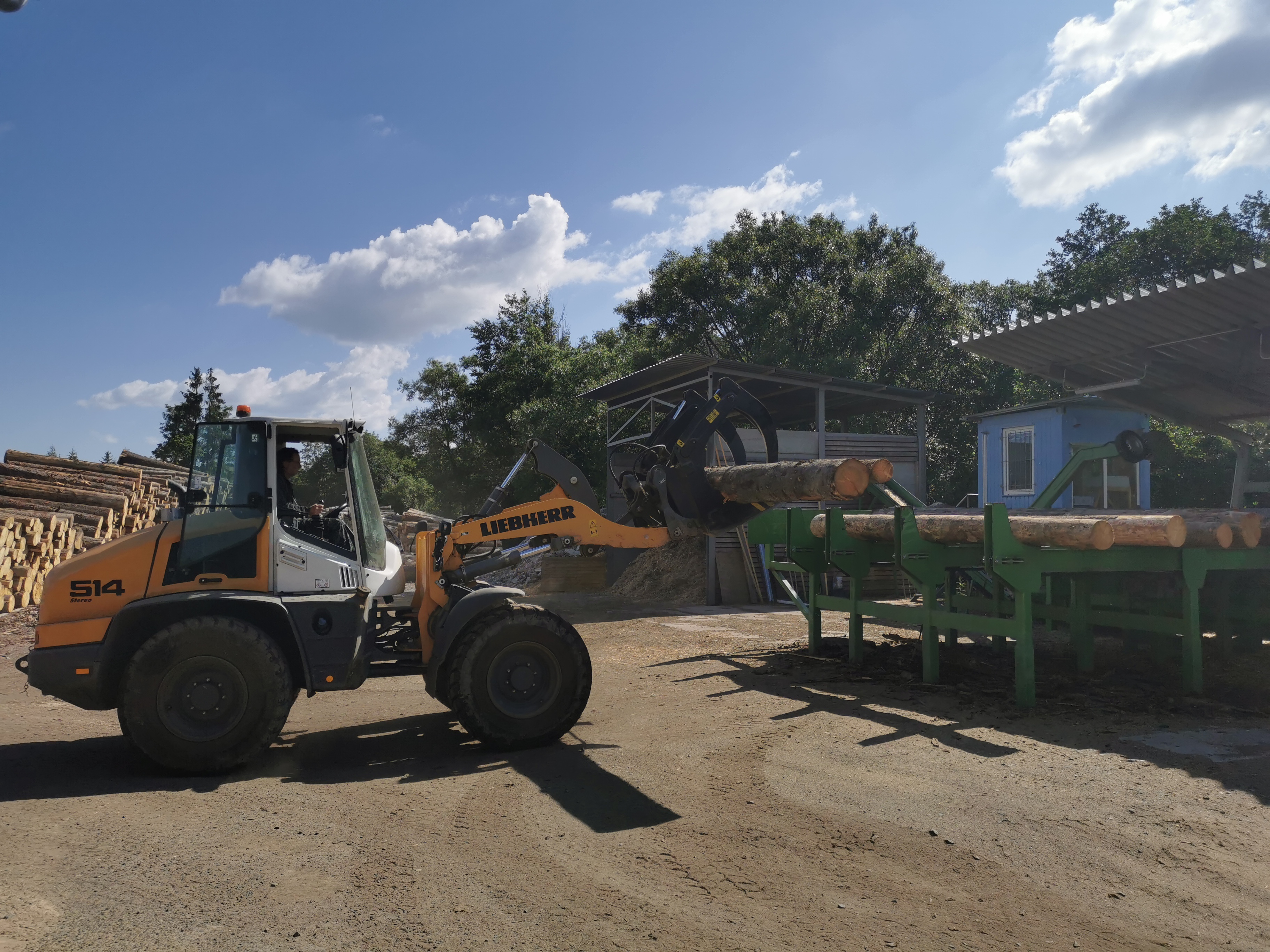
______________________
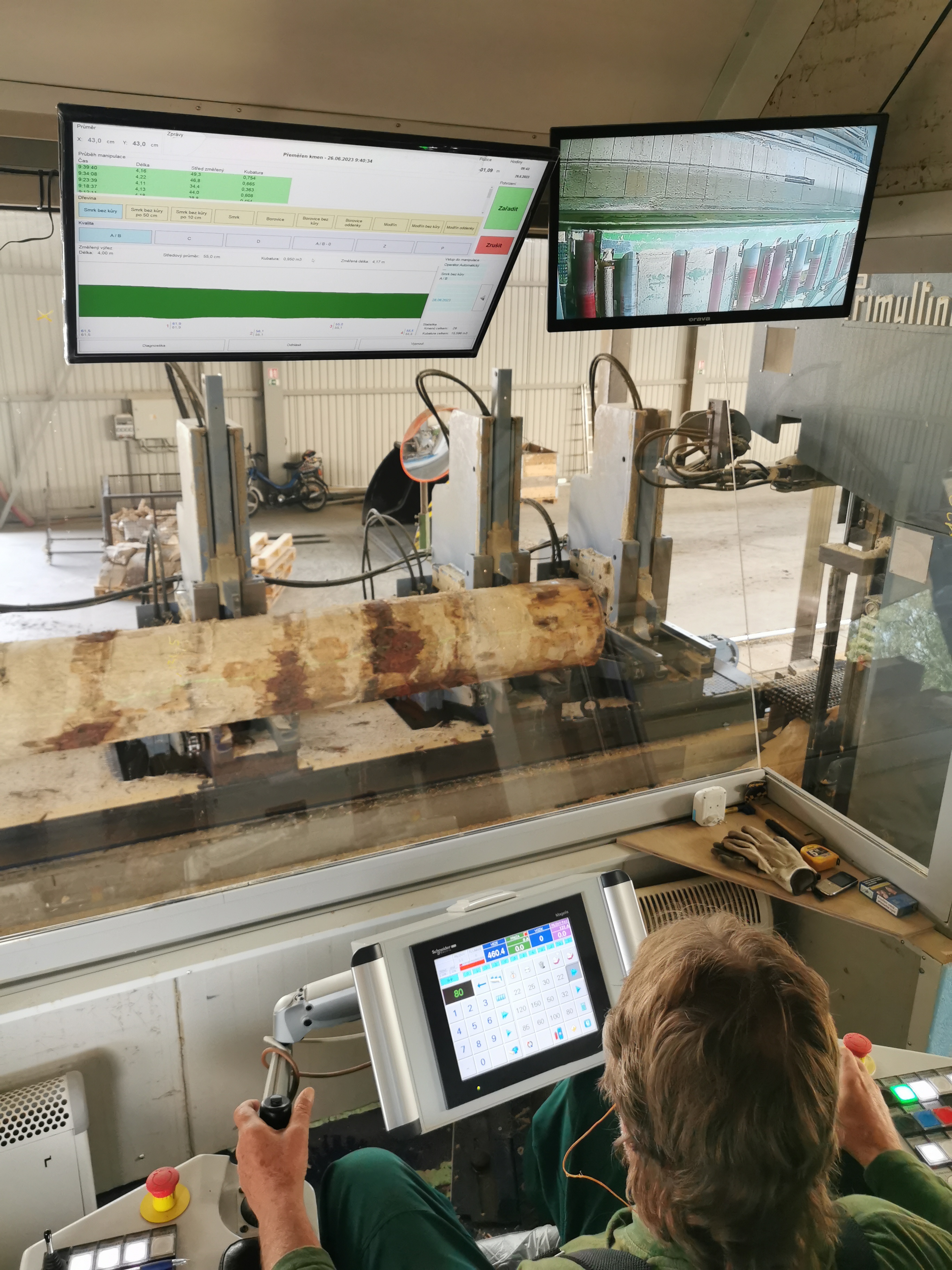
______________________
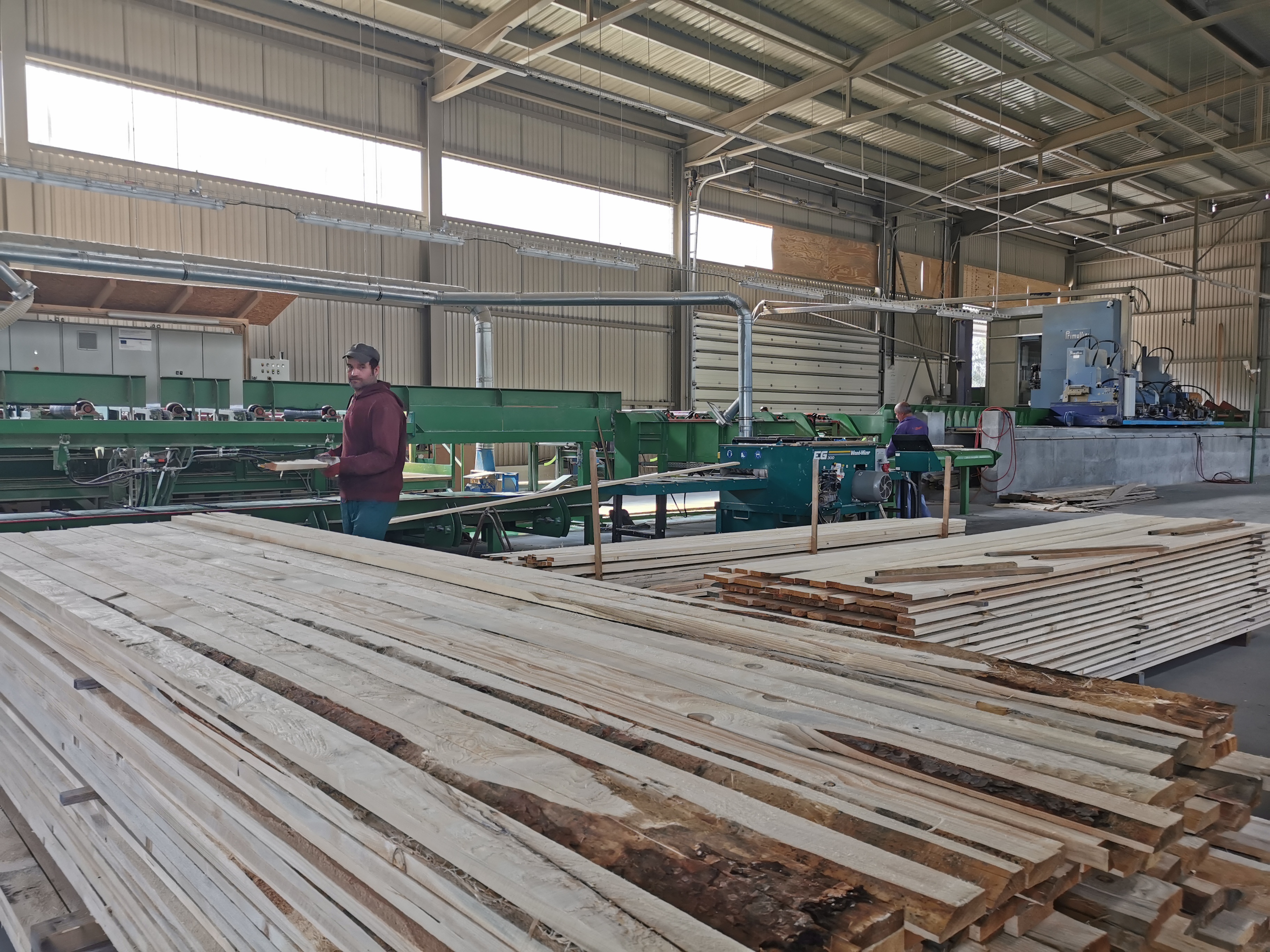
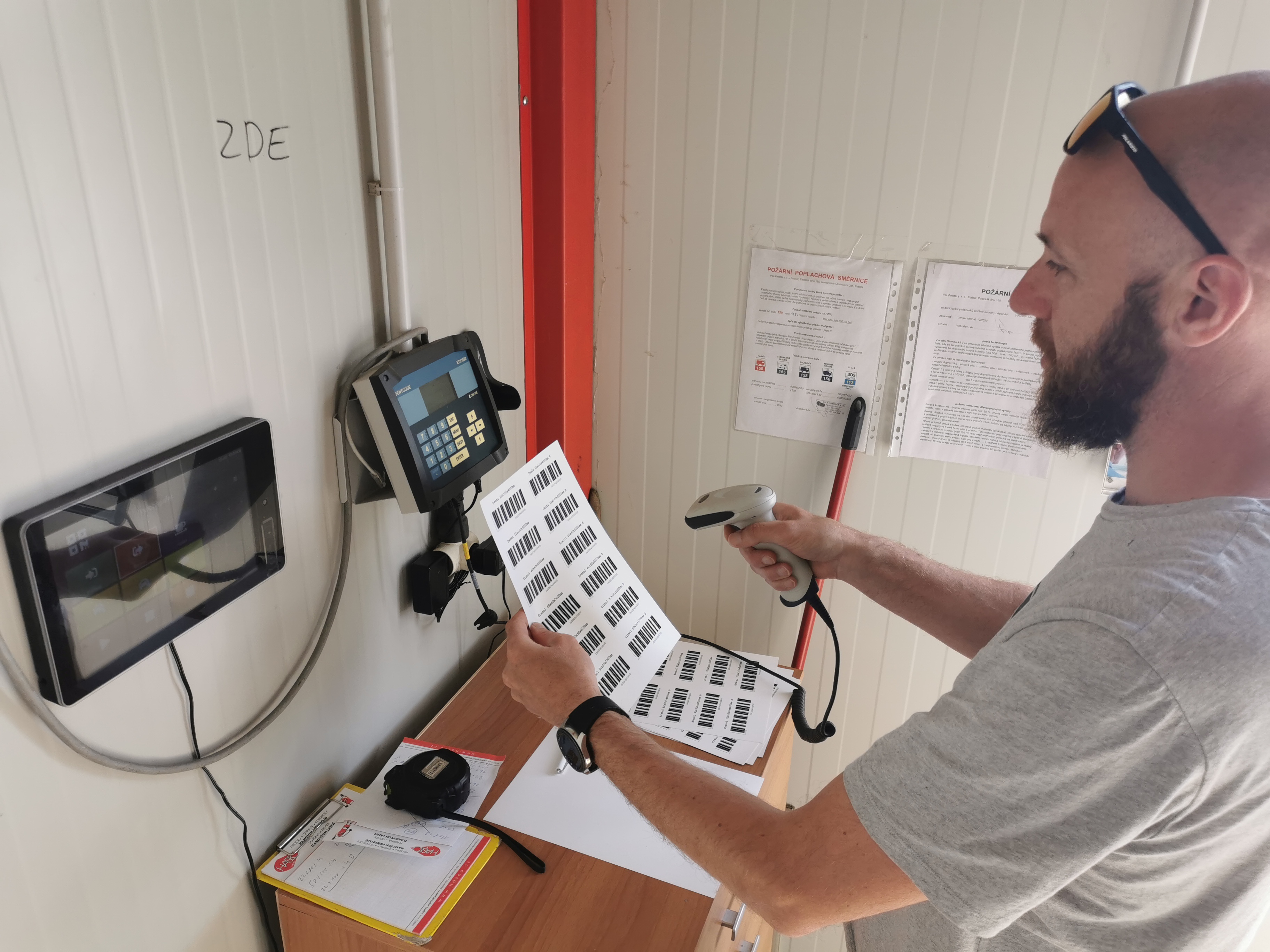
______________________
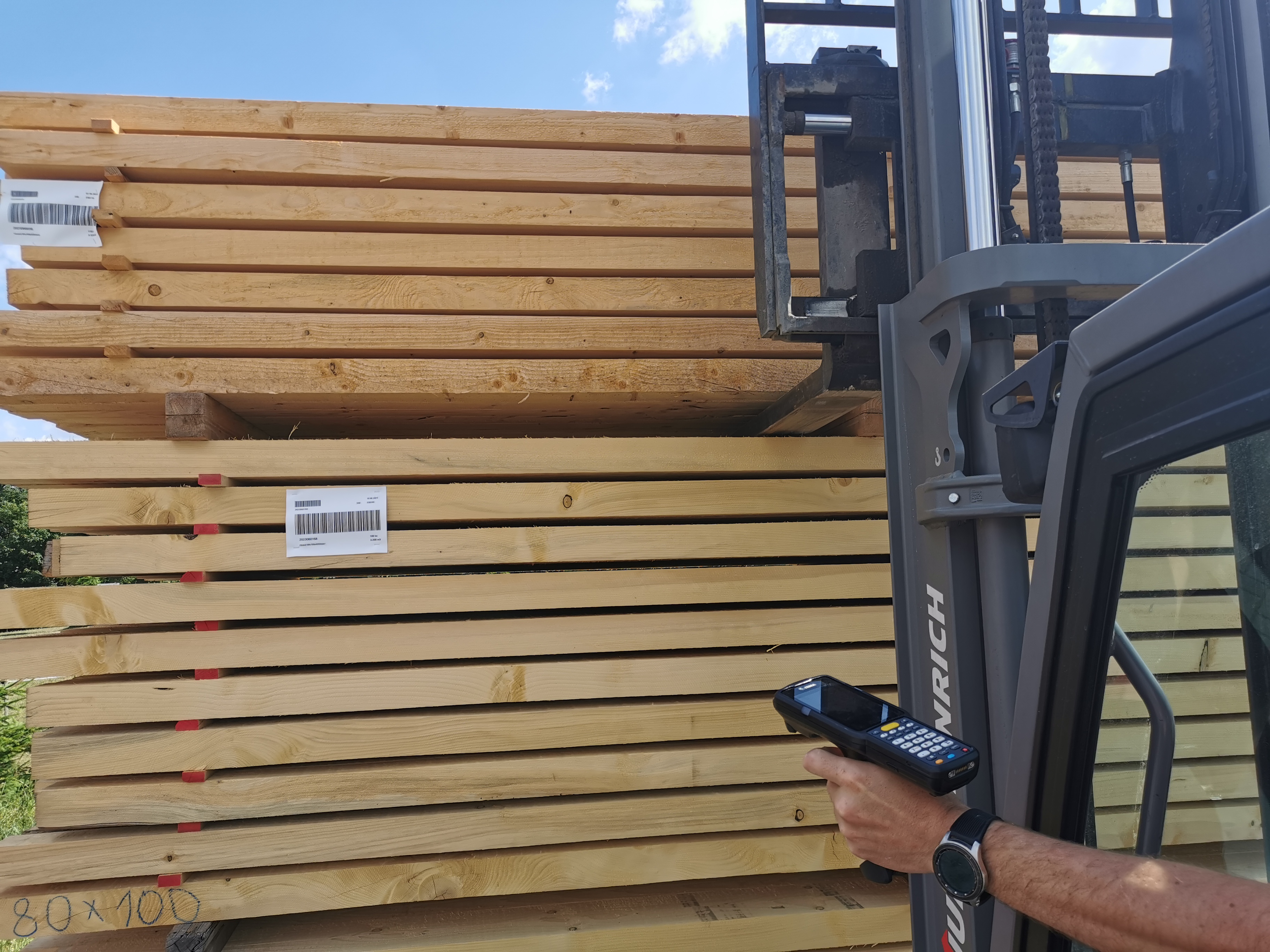
______________________
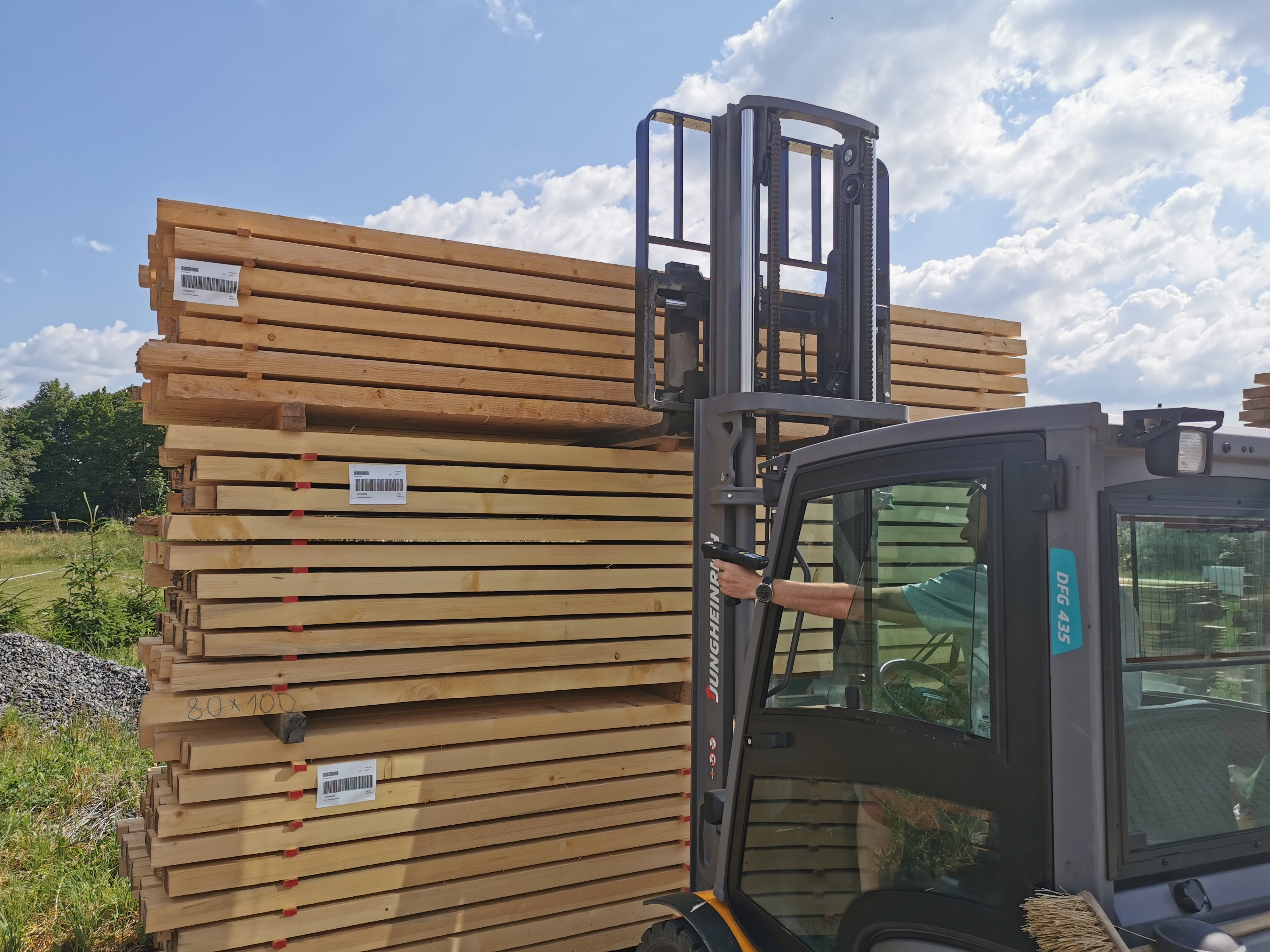
For a material, the alternative can be selected for a specific production order. In the case of complete interchangeability, it is possible to specify that this substitution is valid in general, then the substitution does not have to be written on each production order and it is sufficient to indicate it on the master card.
The first step for the production of the final product - a pallet or wooden packaging - is the preparation of the components for production. Treated or untreated lumber must be cut to the desired lengths in the required number. A "shortening algorithm", which analyses the ordered items in the list of received orders and suggests which lengths of sawn timber to shorten the required parts from, helps with the shortening task. It also works with "inside orders", where a stock of cut lumber is created that will be ready for future orders.
A Shortening Request is created in the information system, which is finalised by the production master taking into account the design of the "shortening algorithm".
The shortening request is printed and handed over to the shortening line operator. Once the request is fulfilled, the cut material is taken to the production component warehouse using a mobile terminal or barcode reader at the stationary terminal and the treated and untreated lumber is written off from the lumber warehouse.
Based on the orders received, the system generates Production Orders. The production foreman schedules them for production. Simple scheduling allows production orders to be designed based on the required delivery dates and in terms of the time required and according to the calculation of the time required for production.
The production orders are given to the shortening line operators who sort the cut lumber according to the Production Orders to the individual production stations.
The production operators then manufacture the final product from the sliced lumber and other components. They can view the production documentation on a mobile terminal or on a stationary terminal. The finished products are transported using the terminals.

The products are ready to be shipped to customers. Each order is marked with its own barcode label to facilitate the dispatch of orders. Each incoming order has an order label with an incoming order number. The purchase order/incoming order number is listed in the Production Order for better visibility.
The actual dispatch is the process where a dispatch/delivery note is issued from the sales order and then an invoice is generated. The documents are sent electronically to the customer.
Incomplete orders can also be shipped with the program tracking the progress of fulfillment.
In case we generate a dispatch from multiple warehouses, multiple delivery notes are generated - for each warehouse.
Orders are linked to both production and invoicing. The company's management has an online overview of key indicators thanks to the implementation of business intelligence, where graphical reports are displayed immediately after the information system is started.
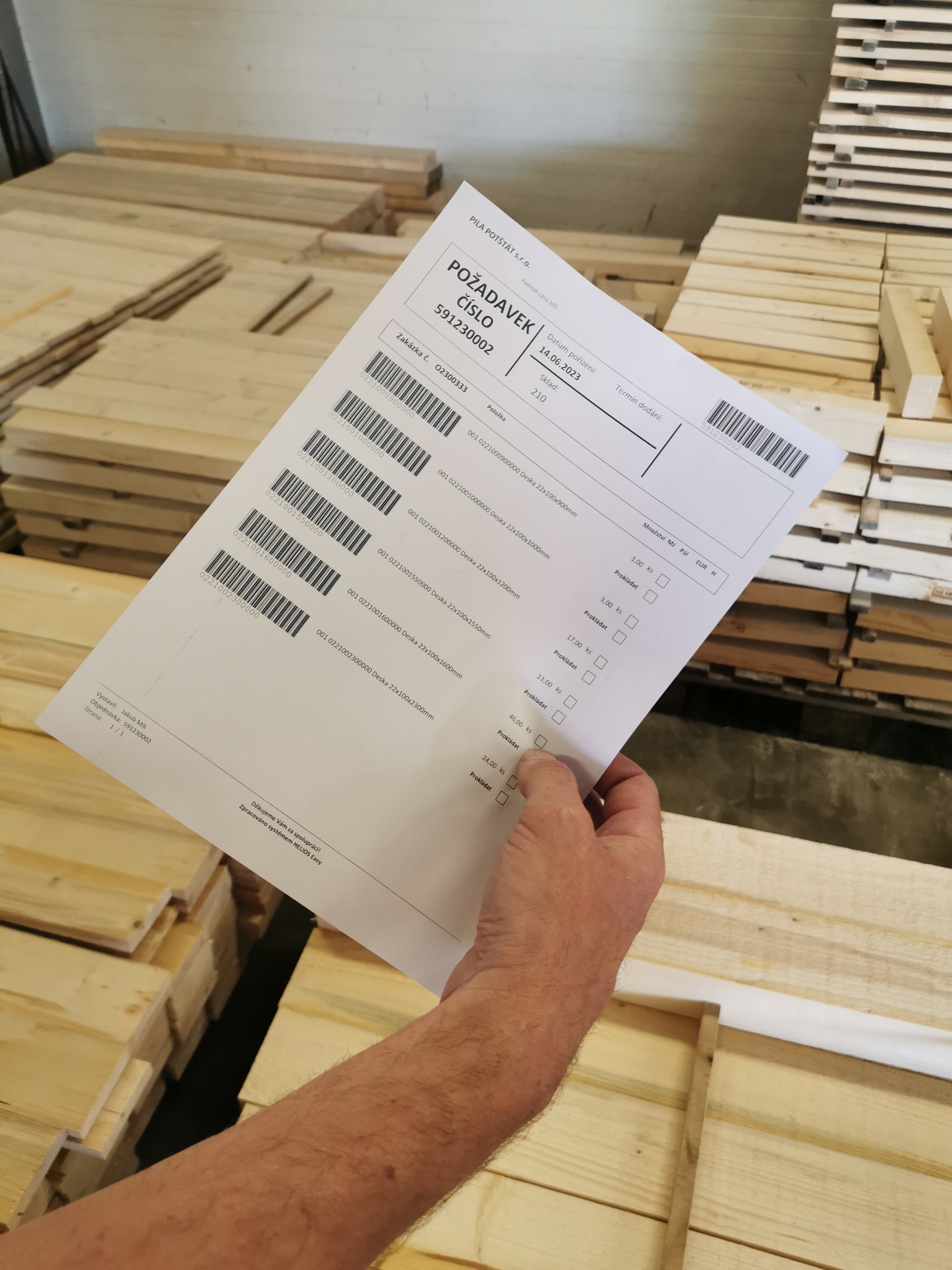
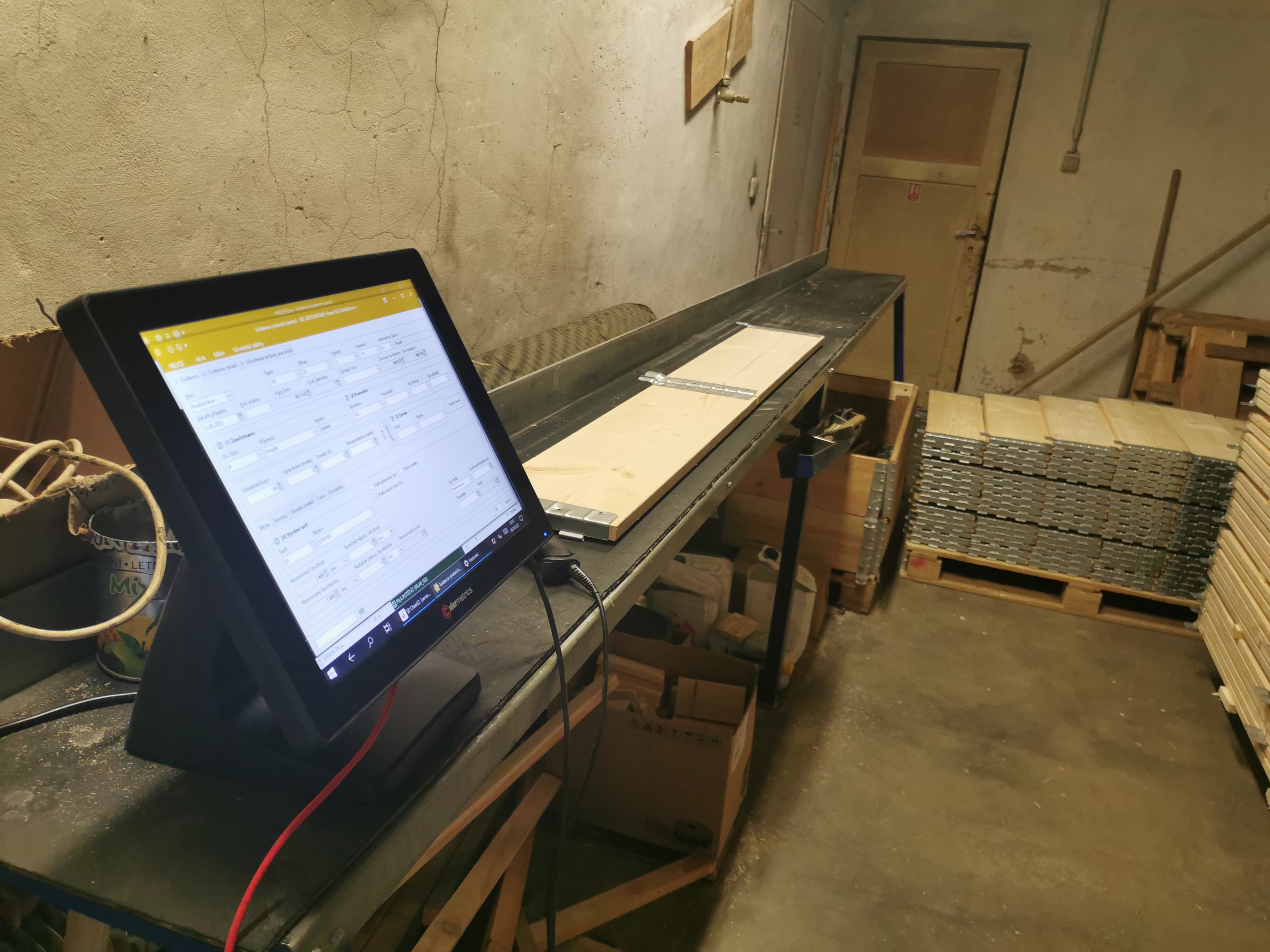
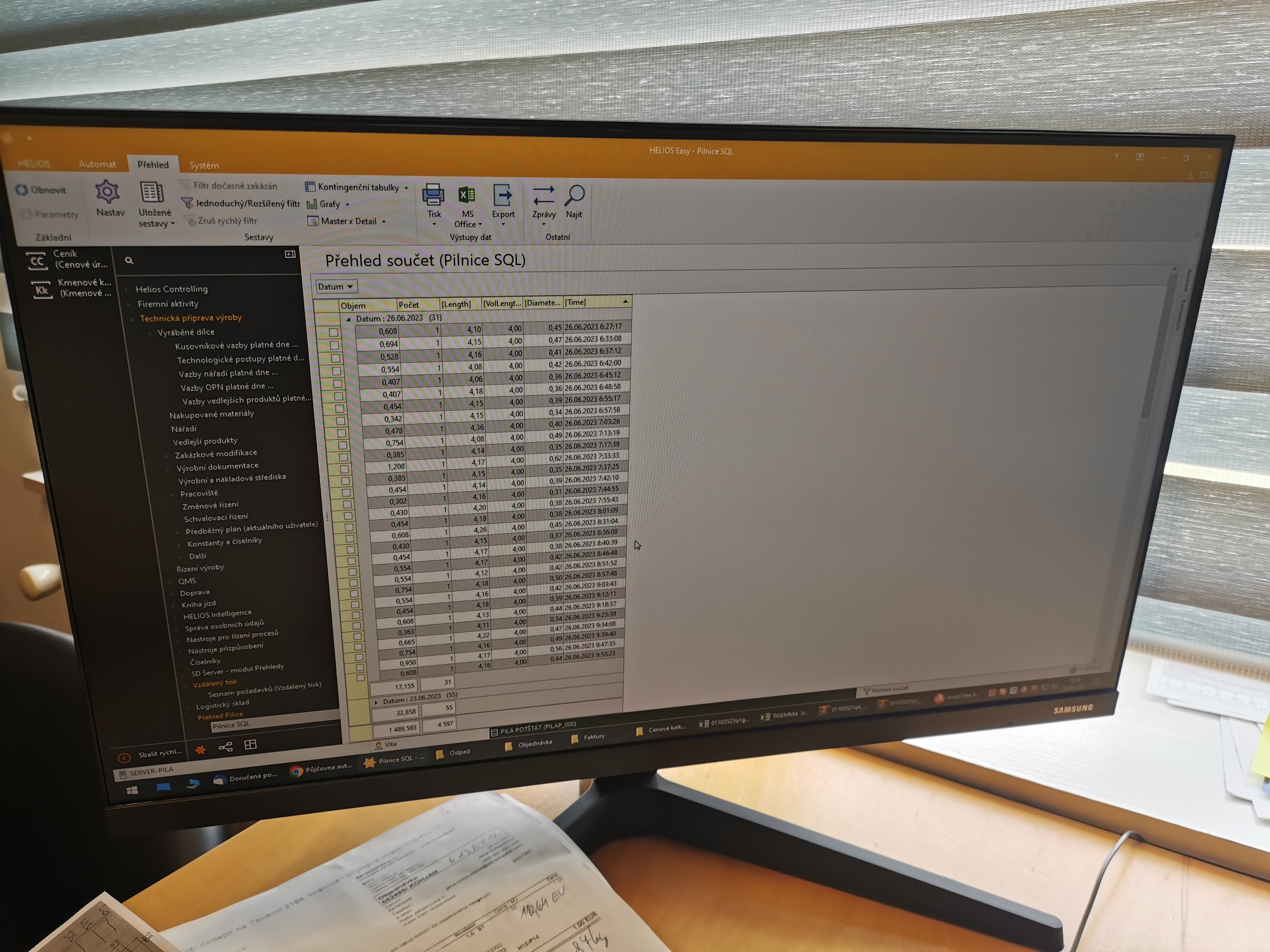
Machine record and attendance
The connection of the machines to the information system is designed for the sorting line, including a milling debarker with a root collar reducer. The information system retrieves information on machine usage (date, hour, log length, diameter and volume) and displays it on-line. It provides an evaluation of the yield for each shift, day, week and month.
A Machinery and Equipment Maintenance module is implemented to ensure automatic preventive maintenance monitoring. The system also works with fault logging.
A cloud-based attendance system GIRITON was purchased for attendance tracking and planning, which is connected to the HELIOS information system. A wall clock with a chip is used to enter attendance. In addition to entering the attendance, the punch clocks, for example, display overtime during chipping, allow to enter and approve requests (for leave, doctors ...), display persons at the workplace and allow to view or edit the shift schedule (according to the user's authorization).
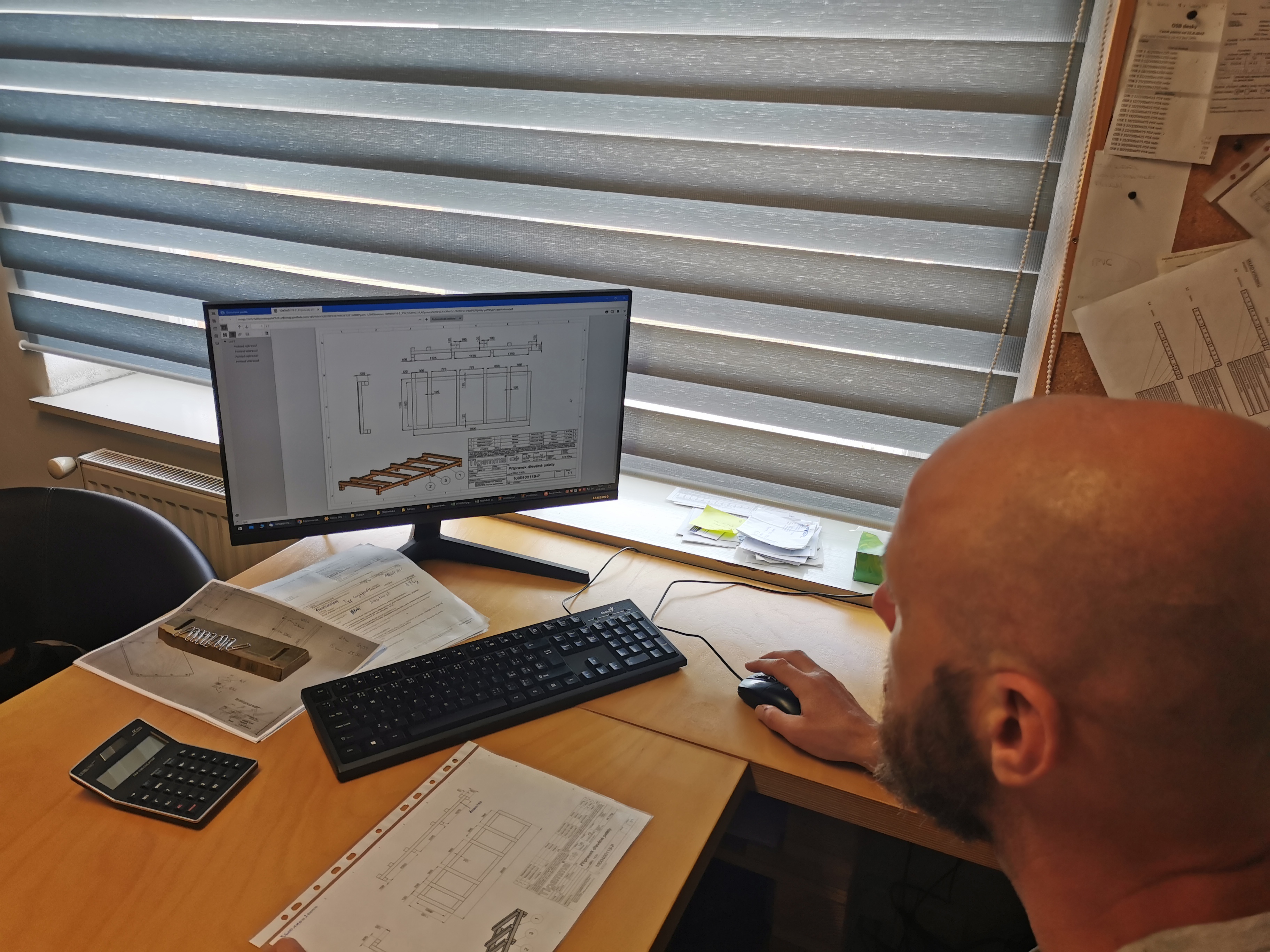
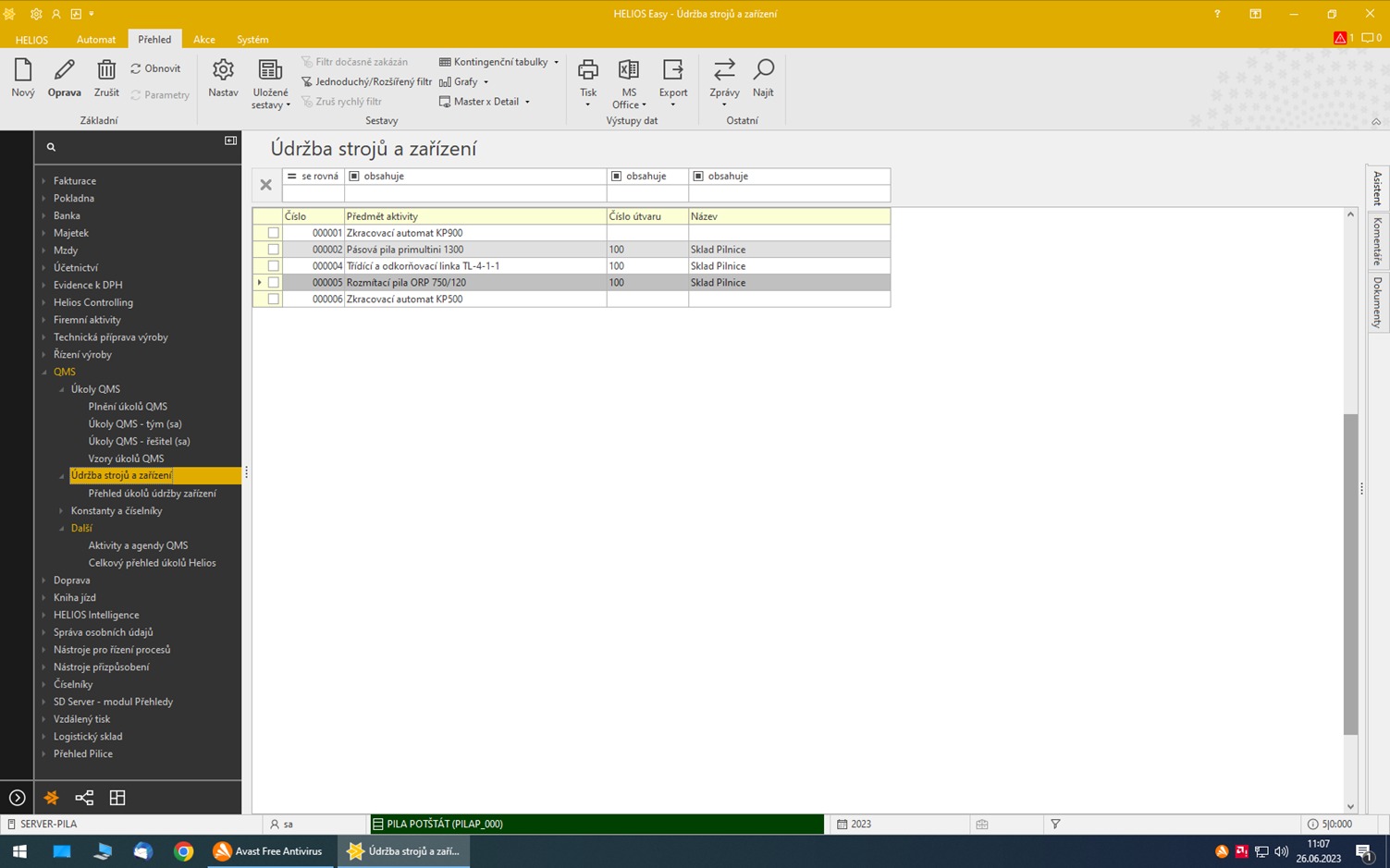
Reporting/Business Intelligence
In the Business Intelligence module, a "digital dashboard" is set up - a managerial interface with graphical overviews of the main company indicators in the areas of economy, orders, warehouses and production.
Data security
The information system can be accessed from any computer outside the company network. The cloud is used for data backup and storage (the proven OneDrive for Business solution within Microsoft 365).
What were the main challenges during implementation?
The challenge was to ensure wi-fi coverage of all production areas. Mobile readers require a constant connection to the network. The control screens on the mobile terminals were modified several times to make the operation as simple and intuitive as possible.
The big challenge was to do a "housekeeping" on the stock cards and to define the individual parts.
We also had to respond to some variability in lumber lengths and quality during implementation.
Afterword
And how does the owner of the company, Mr. Vítězslav Lév, view the new system?
His expectations were mainly:
- Getting an overview of the work done with a link to employee remuneration.
- Obtaining the basis for monitoring the yield of material cutting.
- Overview of the company's inventory and stock levels.
- Optimization of production processes and calculation of optimal cuts according to existing orders.
- Production support and efficiency analysis.
- Simplification of shipping.
- Possibility of remote access to the information system.
- Data security with the use of the cloud for data storage and backup.
"The implementation took longer than we originally expected. Although a fairly thorough feasibility study was prepared, during the deployment of the system we discovered more and more "corners" that had to be solved from the point of view of the information system. The implementation partner HELIsmile s.r.o. always tried to find the most efficient solution", says Vítězslav Lév. He adds: "But the result is worth it. From a managerial point of view, I have data on orders, production status, inventory status and yield data for lumber production."
Implementation: HELIsmile s.r.o.
Implementation took place from 23 May 2022 to 26 May 2023
PILA POTŠTÁT s.r.o., Padesát Lánů 165, 753 62 Potštát, IČ: 27793974
Contact person: Vítězslav Lév, Managing Director, owner
Phone: 606 053 510 E-mail: info@vyrobapalet.cz www.vyrobapalet.cz